Our service division can keep your reverse osmosis water treatment system in tip top condition - even if we didn't supply it!
With an outstanding reputation for honesty and integrity, we support and assist our clients to maintain their equipment efficiently and cost-effectively, using the most sustainable, up-to-date methods in water equipment care.
Not only can we maintain systems that we designed and constructed but the vast majority of other provider's systems as well.
Facilities management experience
Waterforce has more than a decade of experience partnering with large facilities management corporations, subcontracting to provide service and maintenance to essential water treatment infrastructure. Contracts require adherence to safety, quality and timeliness levels.
Over many years Waterforce has proven to be a reliable and trusted supplier, responding quickly to emergency situations no matter the time or situation.
Over many years Waterforce has proven to be a reliable and trusted supplier, responding quickly to emergency situations no matter the time or situation.
Wide variety of trade disciplines
The Waterforce team is comprised of fully qualified electricians, plumbers and technicians working together or separately to fulfill client requirements.
The mix of trades and skill-sets is highly valuable in troubleshooting and resolving issues.
The mix of trades and skill-sets is highly valuable in troubleshooting and resolving issues.
Industry clearances
Waterforce personnel have clearances for Level 2 Security, National Police, Department of Communities and Social Inclusion and Construction Industry White Cards just to name a few.
Safety and environmentally accredited
Rowater Australia is certified for Safety Management System ISO: 45001:2018, Food Safety Program TQCSI HACCP Code: 2003 and Enviromental Management System ISO: 14001:2015.
Optimising existing plant
The combination of Rowater’s three divisions results in expertise that can help clients with site reviews, identifying ways to optimise infrastructure and treatments to maximise water usage.
In many cases the water is used for multiple purposes and, therefore, savings can be made with a holistic approach to the site, leveraging bypasses, chemical treatment and desalination equipment.
Also, providing alternates to expensive equipment replacement is often a topic of discussion.
In many cases the water is used for multiple purposes and, therefore, savings can be made with a holistic approach to the site, leveraging bypasses, chemical treatment and desalination equipment.
Also, providing alternates to expensive equipment replacement is often a topic of discussion.
Seamless transition to new equipment
In circumstances where Waterforce identifies that equipment needs replacing, the team works closely with Rowater engineers to ensure the right solution is developed, the existing system is decommissioned and the new system is installed in a controlled, structured process.
We can service any brand of water treatment system
Waterforce personnel are adept at responding and resolving all kinds of issues, regardless of what brand or model of equipment is in use at the site.
We can work in a wide variety of environments and locations
The Waterforce team are used to rolling up their sleeves and working in all kinds of conditions and locations to ensure the client is back online as soon as possible.
Whether it's working in small plant rooms such as on the sailing ship "The One and All" or travelling to Oodnadatta in the outback, we have you covered..
Whether it's working in small plant rooms such as on the sailing ship "The One and All" or travelling to Oodnadatta in the outback, we have you covered..
We keep an extensive range of spare parts in stock at all times
We know what parts are most likely to be required and keep them on hand, saving you time and money and resolving issues as quickly as possible.
We have remote-access diagnostic capabilities
Our IOT software RO-FIT allows us to remotely access and diagnose issues relating to Rowater equipment (see the RO-FIT page for more information).
We're on call 24/7
We can make out-of-office-hours, emergency site visits in the Adelaide metro area if and whenever they are required.
Alternatively, for regional and national clients, we can trouble-shoot via the phone.
This service offers peace of mind for all our clients.
Alternatively, for regional and national clients, we can trouble-shoot via the phone.
This service offers peace of mind for all our clients.
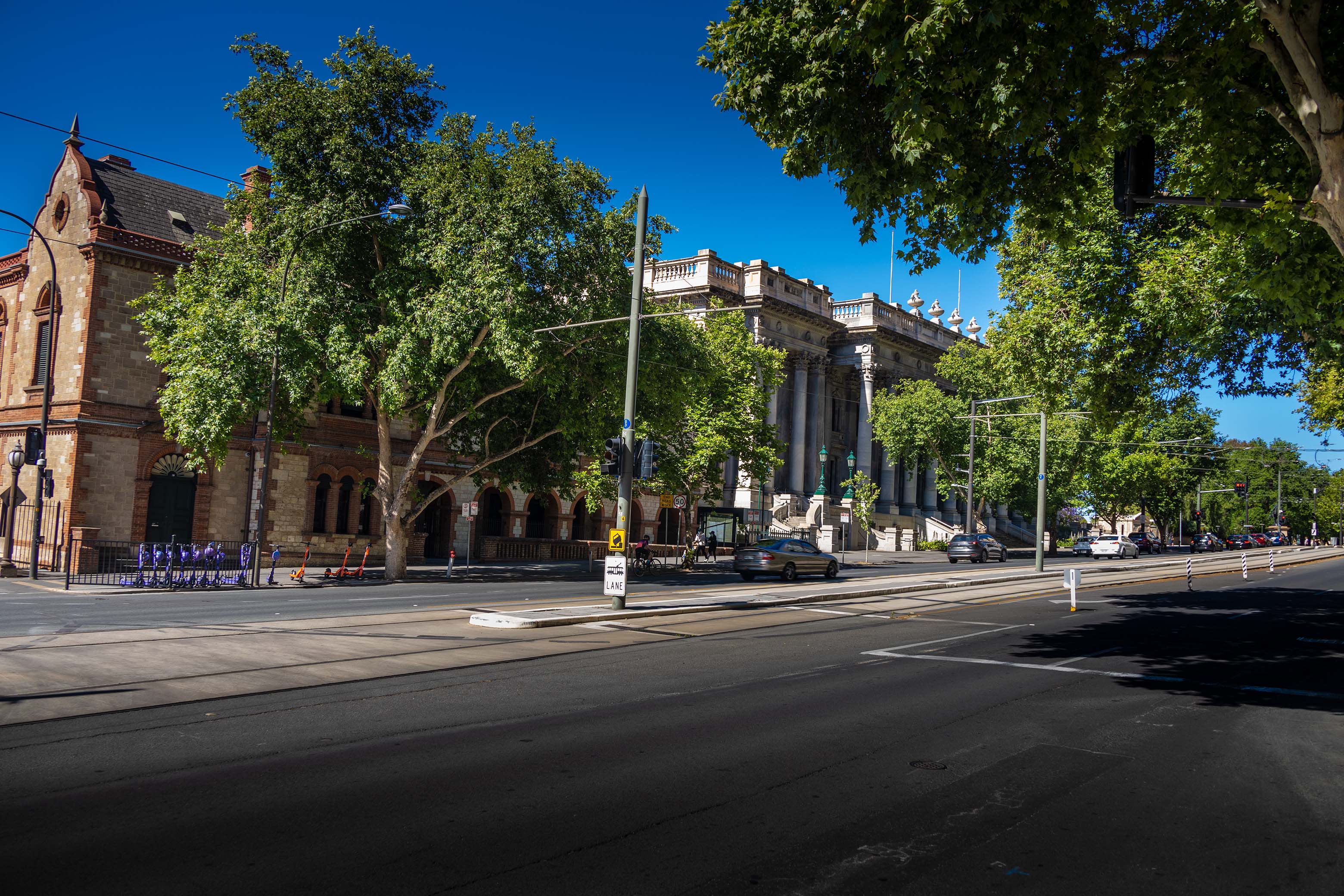
South Australian Government
Rowater provide 24 hour a day, seven days a week support to many state government sites across South Australia.
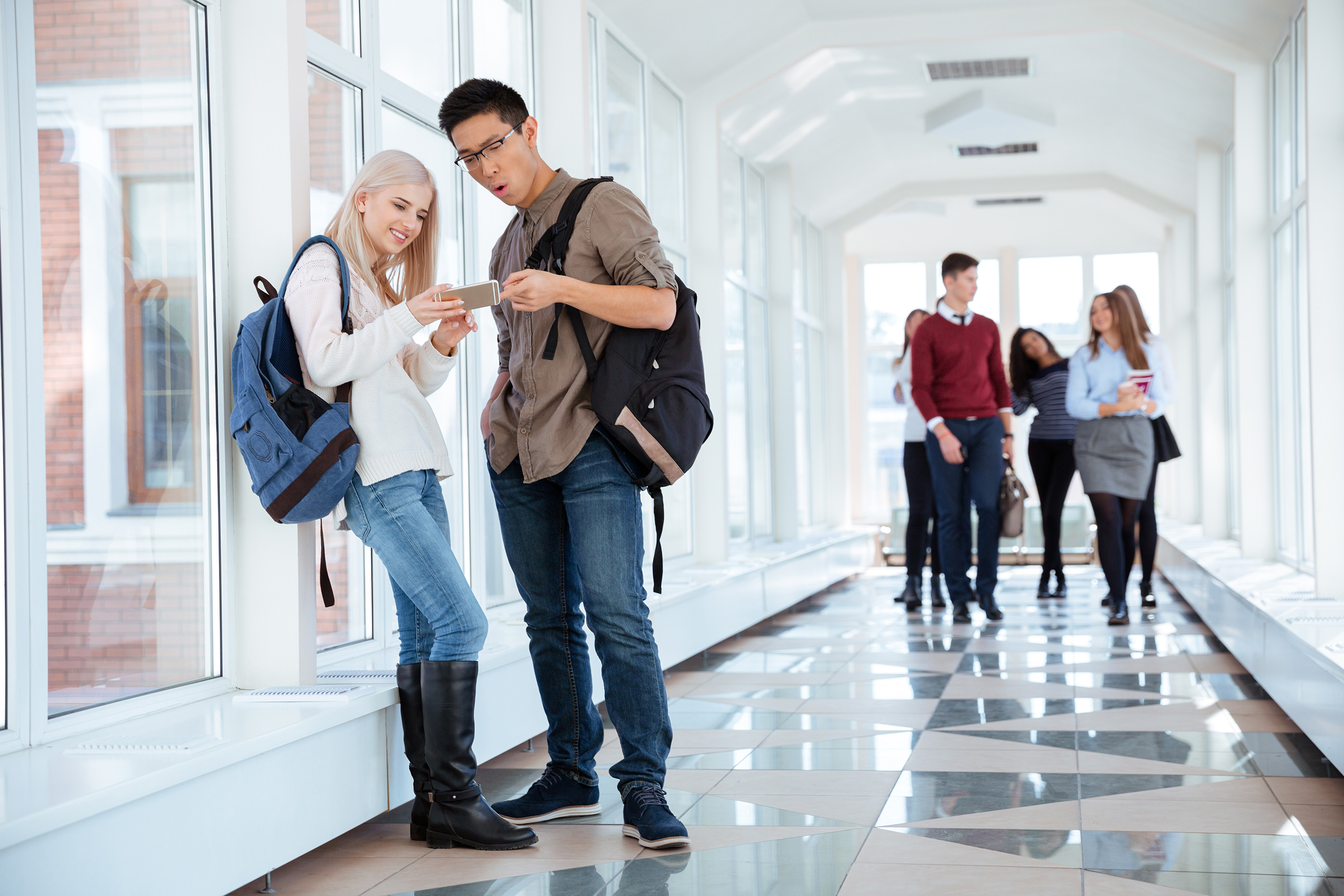
Spotless Facilities Management
Rowater is a proud partner of Spotless, ensuring water treatment systems across Adelaide are kept up and running, 24 hours a day, 7 days a week.
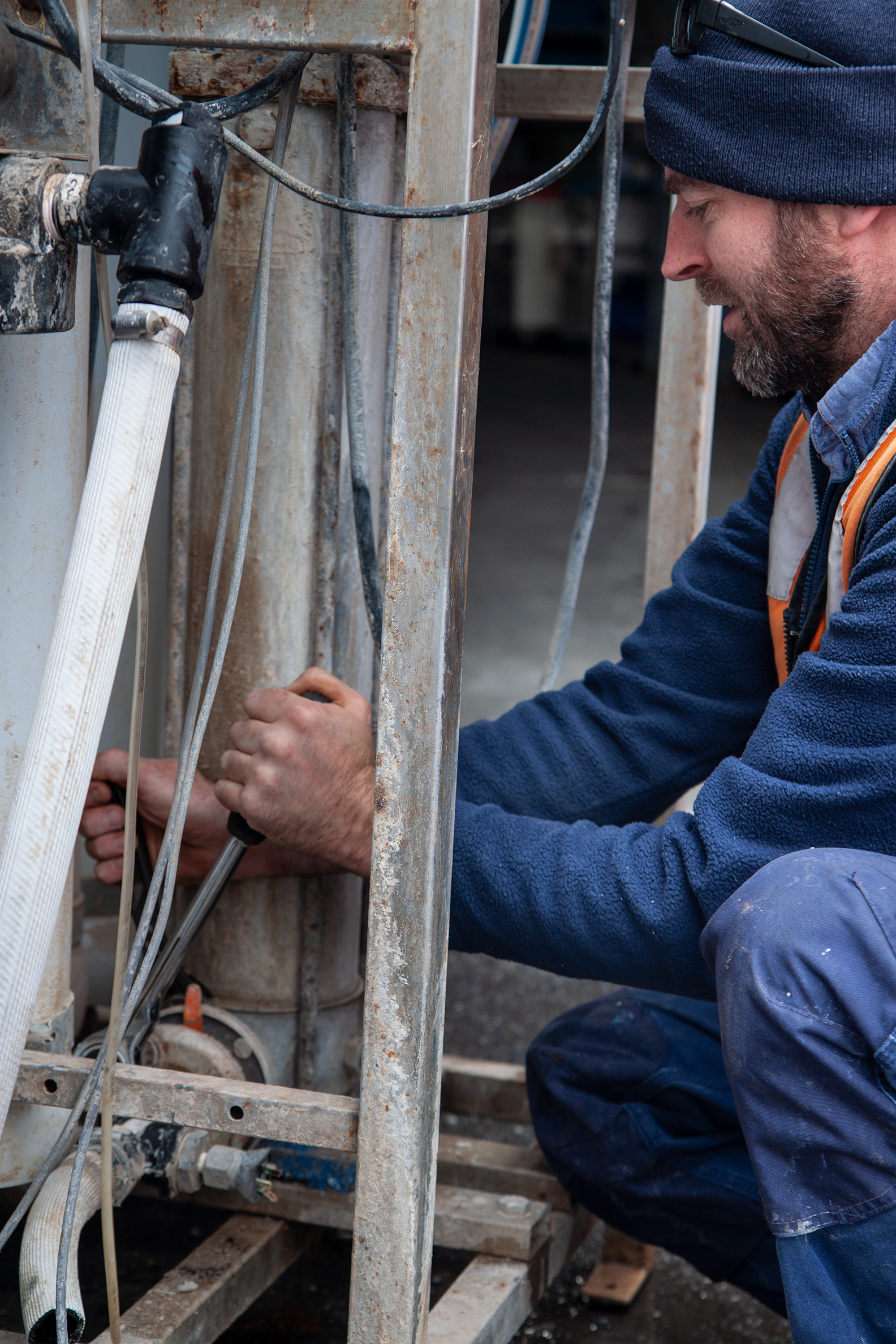
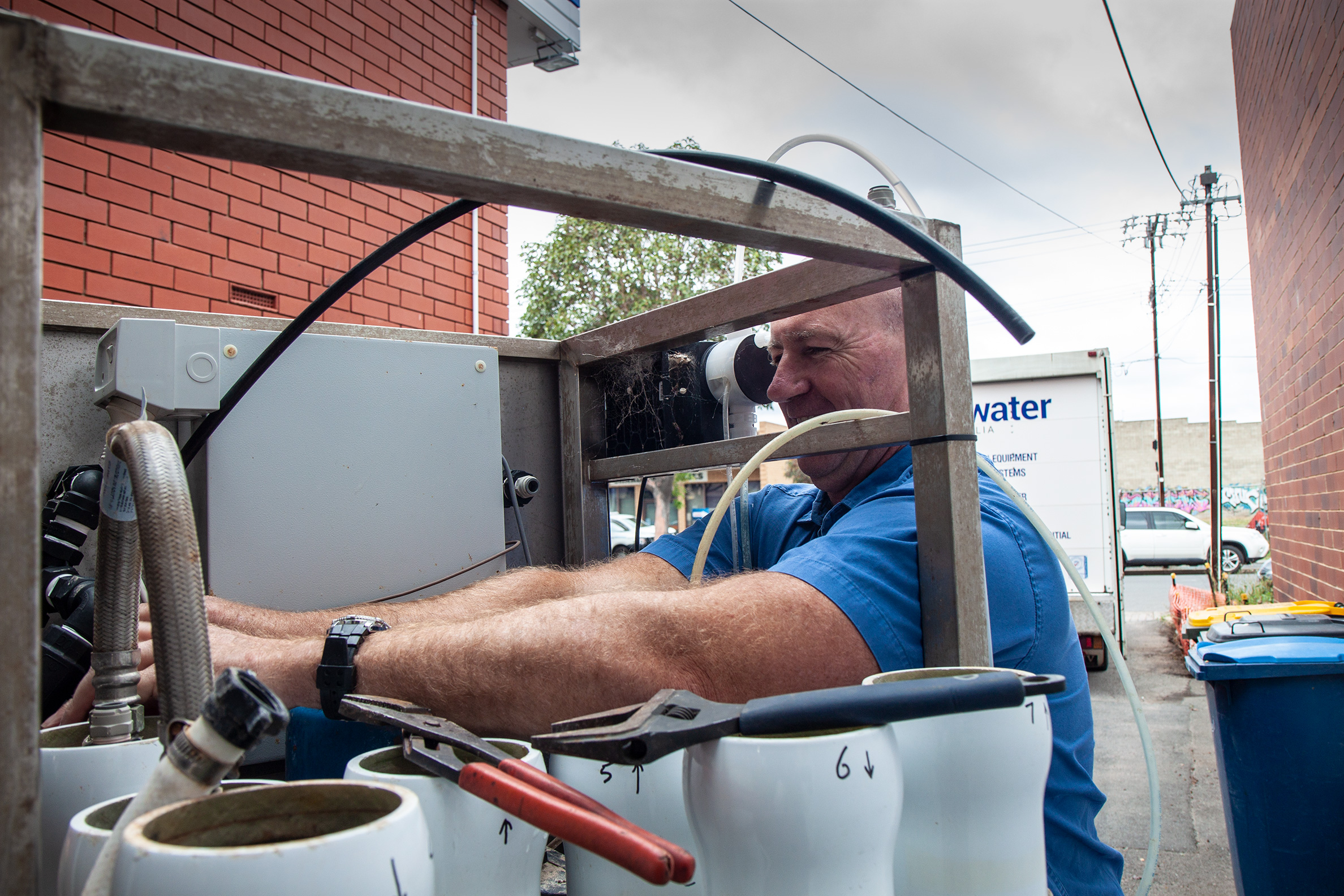